High-stakes at sea require a robust safety culture
09 Nov 2017 Reading time calculated text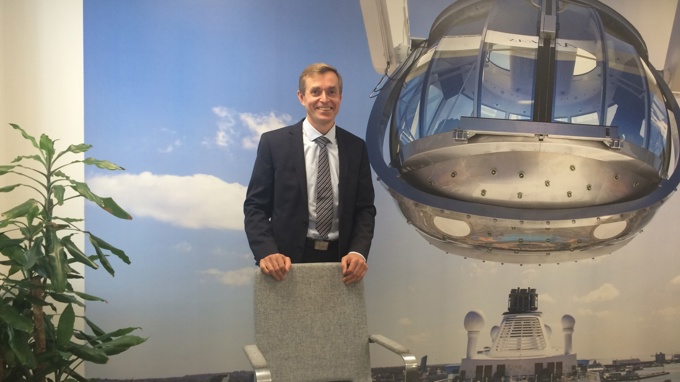
High-value investments, combined with a high-risk environment, set special requirements for marine equipment reliability and quality; a safe industry depends on operators having reliable partners.
At sea, lives, cargo and vessels are at risk of being exposed to the raw elements of nature, as well as that of equipment misuse or malfunction. “There are high-value stakes at sea,” says Tomi Sundell, Cargotec Risk Manager. “Thousands of people sail onboard cruise ships, billion-Euro offshore platforms produce millions of Euros daily, and container ships carry the majority of the world’s global trade. The risks are high – rescue and support can be expensive and far away, so can take a long time to arrive – this is without considering the catastrophic environmental and financial consequences of a major oil spill or accident."
“Operators must have reliable partners for all critical elements of their businesses,” continues Mr Sundell. “This includes the shipyards that build the ships and platforms, equipment suppliers that deliver components, and the workforce for their operations."
“They must also have sufficient redundancy; even if one part fails, others will secure safe operation and business continuity. All parties must be aware of the risks and understand them so that the right risks can be taken. This may sound counter-intuitive, but certain risks must always be taken to achieve the desired objectives.”
Appetite for risk varies
"All marine operations entail risk and we understand that appetite for risk varies. Risk assessment is an integrated part of non-standard or critical projects. We define the scope, identify the risks and their impact. We then look at the probability of them happening and evaluate the benefits of taking the risks against our legal liabilities and also the potentially negative impact on reputation and costs for customers and other stakeholders. If there is not the right balance between the appetite for risk, the likelihood of it happening and the benefits, then we change the parameters until it is worth taking. When all parties understand the risks that need to be taken, they can be mitigated to an acceptable level."
“However,” he explains, “certain risks are unacceptable. These include risks to safety, the risk of non-compliance and the risk of environmental damage".
“We understand that high-value investments at sea, in combination with a high-risk environment, set special requirements for reliability and quality. MacGregor has a proven track record in equipment performance and it takes its place in a chain of responsibility for safety; we all have to work together to maintain and improve safety standards. This is a continuous process within MacGregor.”
Safety in all processes
A true safety culture is built within companies. The biggest improvements in safety records can be seen when companies decide to change their safety culture and implement it throughout all their processes from product development, technical specifications, design, purchase, production, logistics, installation, commissioning and through to operation.
“There are examples when the safety records of companies have improved considerably after an acquisition by a company with a mature safety culture,” Mr Sundell notes. "A change of culture is never easy and fast. It takes time and effort.”
False economies
Many accidents at sea and in port are caused by mistakes, poor maintenance or ingrained bad practices. Well-planned maintenance and training can certainly help eliminate some of these risks. Mr Sundell concedes that during these difficult economic times, maintenance and training may suffer.
“It is a false economy to think that you can economise on maintenance,” he says. “Simple procedures, like failure to grease bearings, can literally result in the collapse of the crane. It is often during emergency procedures, when other equipment may have failed, or in extreme sea states that you need your equipment and crew to perform to their maximum capabilities. Training will ensure this works for the crew and reliable, high-quality, well-maintained equipment will deliver on all other counts".
“As a leading industry supplier, it is important to make training and maintenance attractive to customers and communicate their benefits. Properly trained operators and maintenance personnel improve safety and efficiency by reducing accidents and equipment downtime and by making the most of equipment’s capabilities, you can maximise your profitability. Furthermore, experience and safety records outlining accidents and near-misses can be used to develop operator-specific training,” he says. “It really is a win-win situation.”
Reducing risk
Until now, risk has often been reduced by a conservative approach, which can lead to more expensive operations, but the industry as a whole and MacGregor as a company are looking for smarter ways to reduce risk. The backbone of this will be from advances in digitalization.
“We are continuously looking at ways to reduce risk,” Mr Sundell continues. “One method is remote equipment monitoring. Connecting equipment to the Internet of Things (IoT) enables on-line follow-up and automatic alarms. These advances are part of our digitalisation strategy. We are also well aware of and developing ways to overcome the new risks that inherently come with this territory.”
Safety has to be a priority as industry changes to meet future needs. Traditional bastions of safety in the industry include classification societies, regulatory bodies and Port State Control. P&I clubs and insurers also contribute greatly towards risk management.
“Contracts and insurances are important, but they come into the picture too late, when something has already happened,” he says. “Regulations are also important, but they are often set at a minimum level."
“Regulations are only a starting point for a safe industry. As a leading manufacturer, we not only undertake safety advances within our own product development we also advise rule-makers when there are obvious needs to address troubling safety concerns. For example, the historic series of tragic bulk carrier losses due to a serious underestimation of forces endured by the vessel and its hatch covers; MacGregor voiced its concerns and was strategic in changing the rules.”
Another significant rule change came last year when the IMO amended the Safety of Life at Sea Convention (SOLAS) to require that a container must have a verified weight before being loaded.
“This is obviously good news for safety in the industry; overweight containers have been a high risk for many years,” he says. “Besides losing cargo and containers, inaccurate weights are a high-risk exposure for the ship, crew, other vessels and the environment."
“New regulations can sometimes also create new business opportunities,” Mr Sundell adds. “Leading suppliers and key industry stakeholders, such as MacGregor, play an important role when improving safety. They have the best resources and know-how to develop products and services that drive safety advances."
“We should promote reasonable requirements for safer products and practices towards authorities, customers and other stakeholders. This will set the safety bar higher and could save lives and deliver an advantage to the forerunners that adopt them.”