Ship design should start with earning ability
29 Sep 2017 Reading time calculated text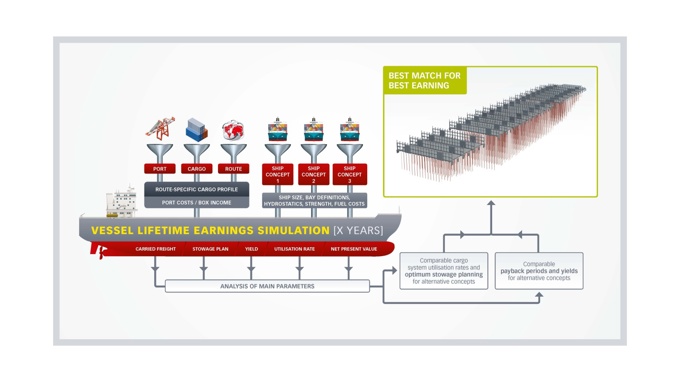
A process that analyses a container ship’s cargo profile is now undergoing trials; it will enable a vessel’s earning ability to be the design starting point, instead of theoretical and unrealistic cargo stowage assumptions
A container carrier’s design starts with the assumption that the cargo, limited by the displacement of the hull, will be homogeneously distributed throughout the ship. As this is not how containers are stowed in reality, MacGregor believes it is time to think differently about cargo stowage.
“Instead of calculating homogeneous maximum stack weights we now calculate a ship’s earnings based on actual cargo profiles,” says Kari Tirkkonen, MacGregor Senior Naval Architect. “A ship’s cargo profile combines information about the distribution of containers on board, their sizes and weights, on a particular route. There has been a clear need for this kind of solution and the development of modern calculation methods now makes it possible.
“With the right design parameters for a vessel and its cargo handling system, MacGregor can maximise the amount of cargo carried in relation to deadweight tonnage. The distribution of heavy and light containers, and subsequently total cargo weight, should therefore be one of the main factors when considering a new ship. We believe that defining the cargo profile should be the cornerstone and starting point for the ship design process and its container stowage. And we set our minds to solving this challenge because we understand the whole cargo system.”
A design process that analyses a container ship’s cargo profile is now undergoing trials. The route-specific cargo profile – based on port, cargo and route information – is evaluated against alternative ship concepts, considering, for example, the vessel’s operational expenditure (Opex) and the cargo system’s capital expenditure (Capex).
“Our target is to help make this mindset change…But the earning ability of the ship must be the starting point and key issue”
- Kari Tirkkonen
The vessel’s operations can be simulated over a given number of years for alternative ship concepts. “As a result of this simulation, we obtain a number of main parameters,” Mr Tirkkonen explains. “After analysing these, we are able to design the optimum stowage concept, resulting in the best match for the ship’s route, with some built-in flexibility”.
“We use a statistical method for analysing the cargo profiles of customers’ newbuildings and the analysis results are used to define the required cargo handling systems. This approach is rather new in the industry,” says Janne Suominen, Manager, MacGregor Cargo System Development. “The project comes to an end this year. Everything looks good so far, but we are being cautiously optimistic until we finish.
“We hope to deliver a tool that predicts and delivers maximum profitability from a ship’s ‘earning machinery’. It will mean that we can help customers make the best decisions at the investment phase. “It is also self-evident that an efficient cargo handling system minimises emissions for each carried commodity, which reduces their carbon footprint,” Mr Suominen adds.
The statistical review of the cargo profile enables the productivity of different cargo systems and ship concepts to be compared. The process has two main elements, the stowage planning module and the cost model.
The stowage planning module gives a comparable utilisation rate of the cargo system. Variables such as ship data, bay definitions, hydrostatic and strength data, route data, port data and cargo mix are entered, and the plan produced is checked against MacGregor’s Lashmate stowage calculation software.
The cost model produces information about comparable payback periods and yields, delivered as a comparative net present value between two vessels. Investment, operational expenditure and revenue are also taken into consideration. Input data includes program control settings such as the number of average operable days per year, crane properties, vessel data, route data including ports of call, leg distances and freight rates, port data, and other information such as fuel costs.
“The analysis is specific to a vessel, but the benefits of scale can be reached if the whole fleet is analysed in the same way,” notes Mr Suominen.
Mr Tirkkonen says: “We can help customers to think about how they make money with a ship, not just about its order price from the shipyard. It is a simple fact that it pays off to invest a little more in the ship and a better cargo system. The payback time is shorter, which means it starts bringing in more money sooner. The cost efficiency of the investment is improved.
“Our target is to help make this mindset change together with our customers, both shipyards and shipowners. It is of course in a yard’s interest to fabricate the ship as cost-efficiently as possible, and we understand that aspect as well. But the earning ability of the ship must be the starting point and key issue.
“The analysis is specific to a vessel, but the benefits of scale can be reached if the whole fleet is analysed in the same way”
– Janne Suominen
“This approach is not just for newbuilding projects,” adds Mr Tirkkonen. “If a customer contacts us about a year before drydocking, we can produce a plan on how to enhance a vessel’s cargo system to better meet actual needs. We already have a number of enquiries from customers who are interested in employing the benefits of this new approach.
“Also because vessels are re-located to operate on different routes, when designing the ship, consideration must be given both to the initial cargo profile and to the flexibility necessary to accommodate possible future changes to the cargo profile”.